Class10.9 Bolt Manufacturer, Supplier and Factory In China
Ningbo Teng Qi Fasteners stands as a leading manufacturer specializing in the production of class10.9 bolts. Leveraging advanced techniques such as cold heading and hot forging, we offer an extensive size range from M0.8 to M100, addressing a diverse spectrum of industrial needs.
Our commitment to excellence is reflected in our material choices, encompassing high-quality carbon steel and alloy steel. This ensures that our class 10.9 bolts exhibit exceptional strength and durability, meeting the stringent requirements of high-stress applications.
With a focus on surface treatments, we provide a range of finishes such as black oxide for a refined appearance, galvanization for corrosion resistance, hot-dip galvanization for augmented durability, and zinc flake coatings for prolonged protection.
Ningbo Teng Qi Fasteners, drawing on 20 years of industry leadership, delivers precision-crafted class 10.9 bolts that stand as a testament to reliability and performance across diverse industrial sectors.
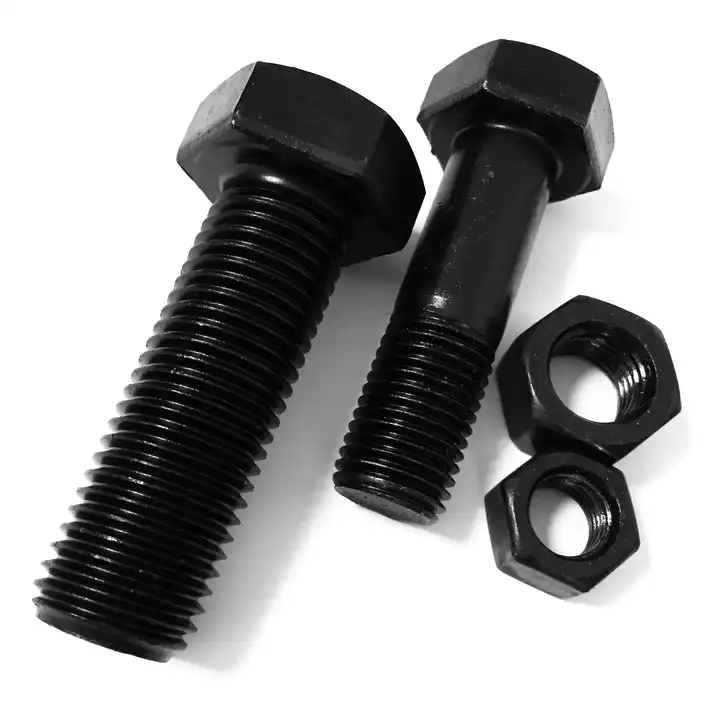
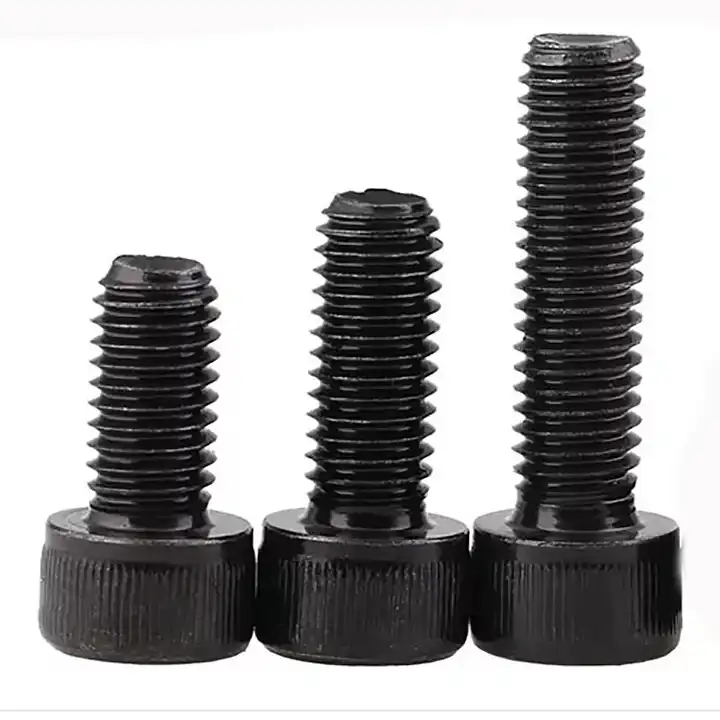
Specification of Class10.9 High Strength Bolt:
The specification of an class10.9 high strength bolt refers to its specific dimensions, thread pitch, and other mechanical properties.
Product name | Class10.9 Bolt |
---|---|
Size: | Metric: M0.8-M100 |
Length: | Metric: Up to 800mm |
Material: | Alloy Steel(42crmo,35crmo) |
Strength Grade: | 1040 MPa (min) |
Head Type: | Hex Head/Socket Head/Countersunk Head/Round Head/Flat Head |
Industry Standards: | ISO/ASTM/ASME/DIN/UNI/JIS |
Packaging: | Boxes/cartons into wooden pallets |
Application: | Construction/Automotive/Marine/Aerospace/Food and Beverage Industry/Medical Equipment/Chemical Processing/Water Treatment |
FAQ about Class10.9 Bolt:
1. Q: Are your class 10.9 high-strength bolts compliant with industry standards, and do you provide certification?
A: Yes, our bolts strictly adhere to industry standards such as ISO 898-1.
2. Q: How is the manufacturing process meticulously controlled to ensure precision and consistency in the production of class 10.9 high-strength bolts?
A: Our manufacturing process is characterized by rigorous controls at every stage, ranging from cold heading and hot forging to the final inspection. This ensures precision and uniformity in every high-strength bolt.
3. Q: What measures are implemented in your quality control during the manufacturing process to promptly detect defects or inconsistencies in class 10.9 high-strength bolts?
A: Our quality control entails regular inspections, dimensional checks, and testing of mechanical properties, enabling the prompt identification and resolution of any defects or inconsistencies.
4. Q: What surface treatment options are available for class 10.9 high-strength bolts, and how do these treatments impact performance?
A: We offer a variety of surface treatments, including black oxide for a refined appearance, galvanization for corrosion resistance, and zinc flake coatings for extended protection. These treatments enhance both functionality and durability.
5. Q: Is there a warranty or guarantee for the performance and durability of your class 10.9 high-strength bolts?
A: Yes, we stand by the quality of our bolts. For details on warranties and guarantees, please reach out to our customer service team.
Quality Control of Class10.9 Bolt:
Control Method | Detail |
---|---|
Material Inspection: | Verify the material's composition, heat treatment, and quality upon receipt. Conduct metallurgical analysis to ensure the material properties meet the standards. |
Process Control: | Implement strict process control measures for heat treatment, machining, threading, and any other manufacturing steps. Maintain consistent process parameters to ensure uniform quality. |
Inspection Points: | Introduce inspection points at various stages of manufacturing to check for defects, dimensions, and quality. Inspect threading, dimensions, surface finish, and other critical parameters. |
Sampling and Testing: | Regularly sample products for testing, such as tensile testing, hardness testing, and metallurgical analysis, to ensure they meet the required specifications. |
Thread Inspection: | Thoroughly inspect threading using proper thread gauges to ensure accurate dimensions and fit with mating components. |
Traceability: | Implement a traceability system to track each fasteners journey from raw material to final product. This aids in accountability and recalls if necessary. |